MPCNC
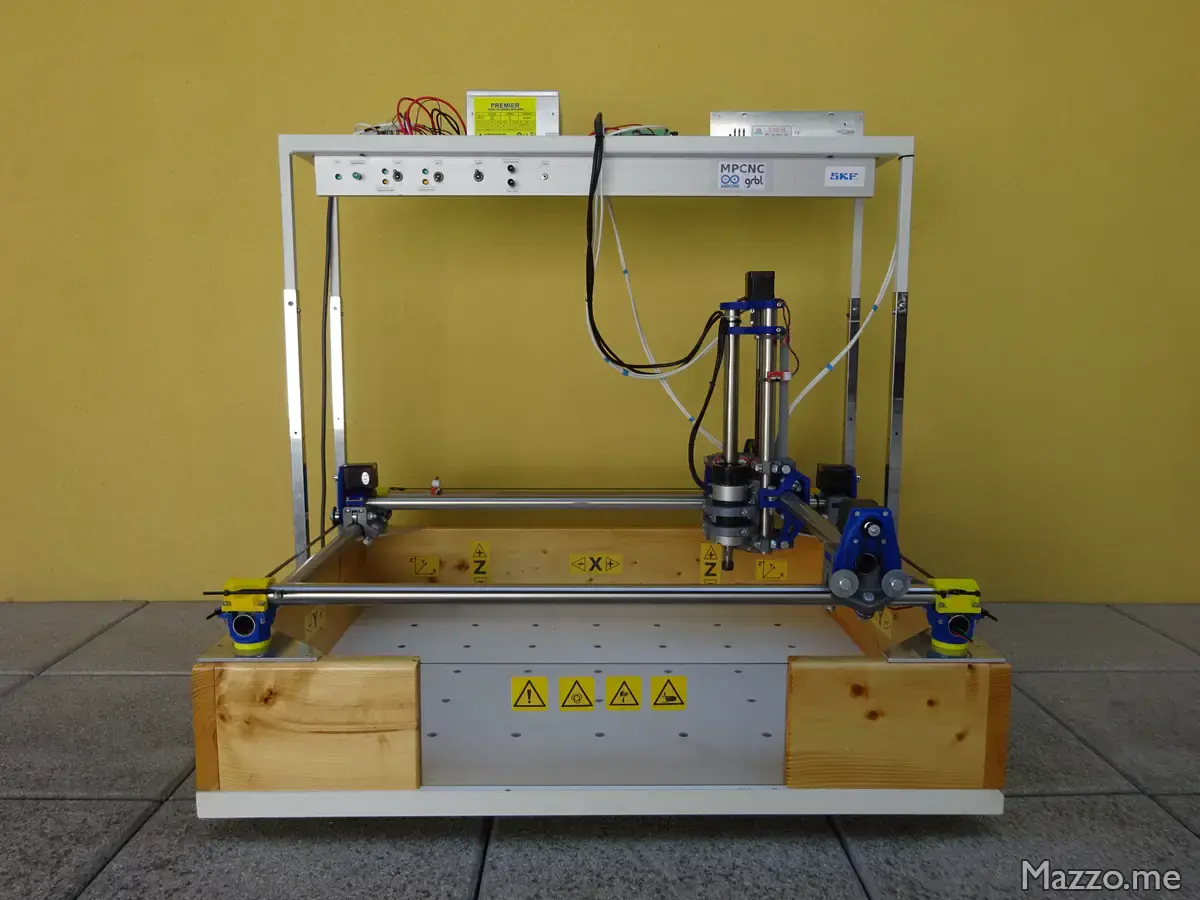
I built this computer numerical control machine based on the original project of V1 Engineering. I made some changes such as a wooden frame, a work plan and a control panel to manage the electronics.
The 3D printed elements that are part of the structure were made with my 3D Printer.
It is equipped as a light milling machine, with a 400W brushless spindle motor that allows me to mill soft materials such as wood and polystyrene, but also to perform some work on harder materials such as aluminum and brass.
The axes are made with stainless steel tubes and are moved by stepper motors with belt movement, while the electronics is based on an Arduino with GRBL firmware.
The front of the frame can be opened removing a plexiglas wall:
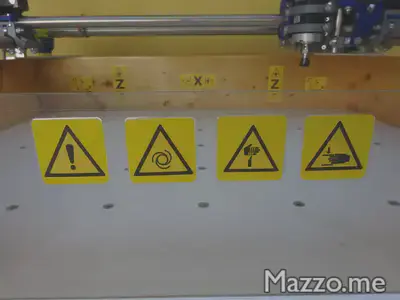
The belts are stretched with cable ties:
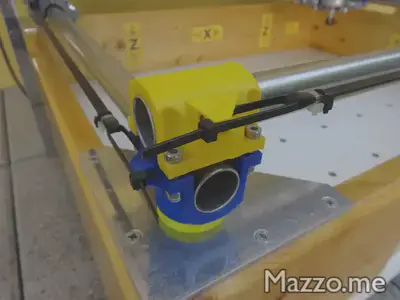
The structure is screwed to the frame with aluminum plates:
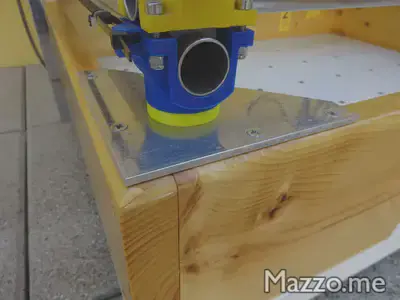
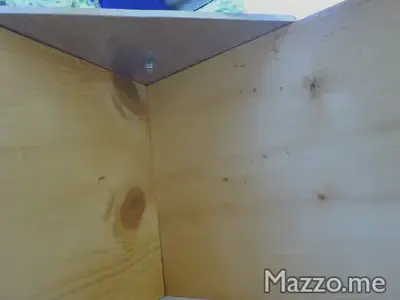
The axis movement is belt driven:
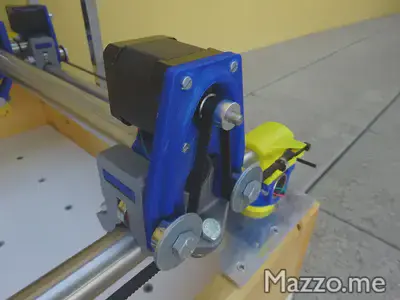
The motor cables pass inside the tubes:
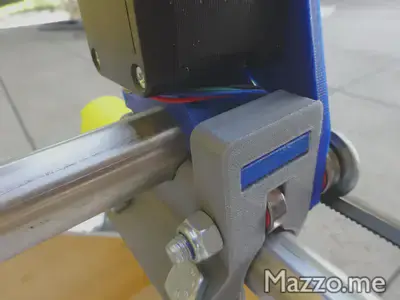
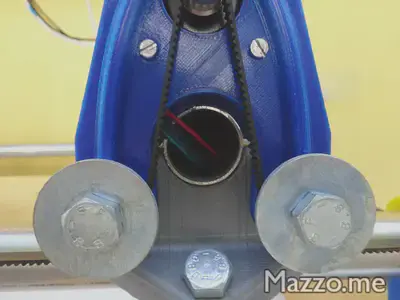
As well as the limit switch cables:
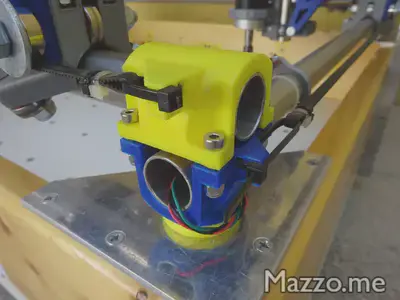
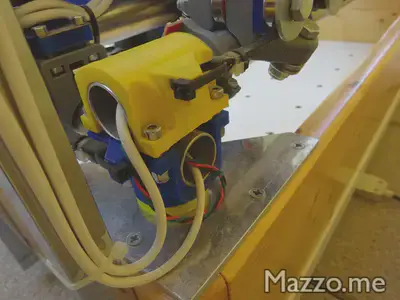
The central part that joins the three axes is printed in 3D:

The brushless spindle motor is fixed with 3D printed supports:
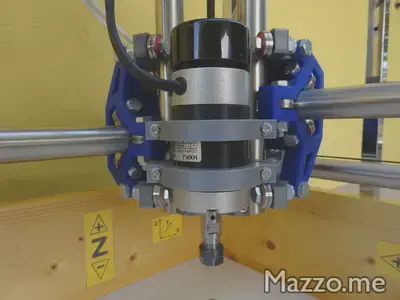
And it has an ER11 chuck that allows me to take tools with diameter up to 7 mm:
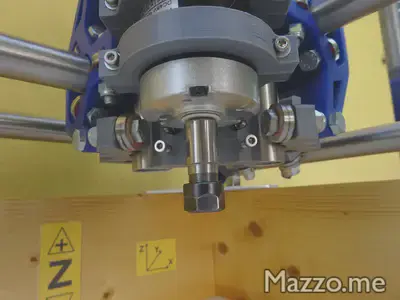
The Z axis has a useful stroke of about 100 mm:
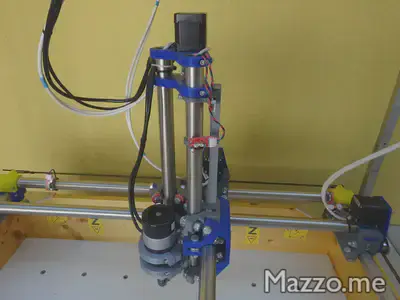
On all the axes both upper and lower limit switches are present:
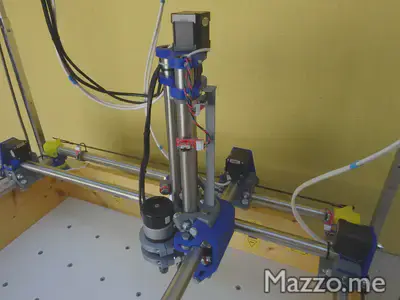
For the upper limit switch of the Z axis I made an apposite stop:
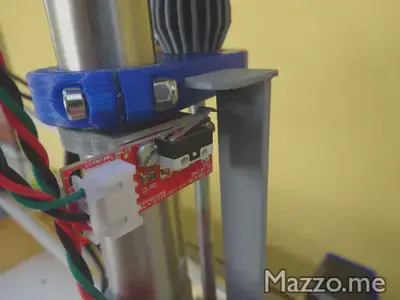
The Z axis motor coupling is 3D printed:
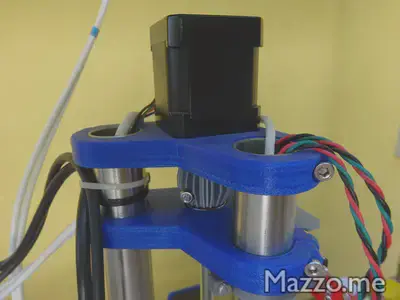
The limit switches are attached to the sliding tubes:
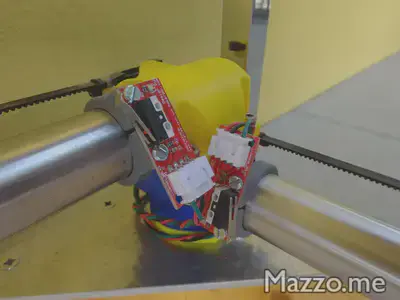
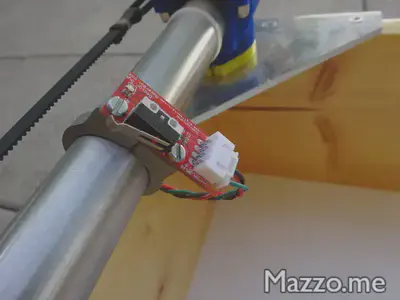
The control panel is equipped with buttons, switches, indicator LEDs and touch probe connector:
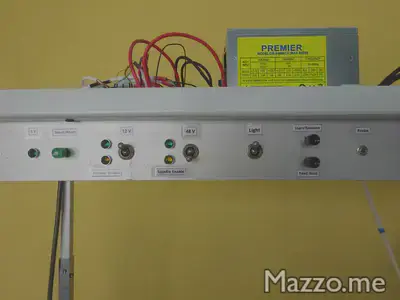
The electronics is drived by an Arduino and has a DRV8825 driver for each motor:
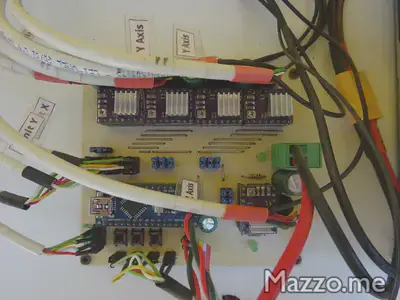
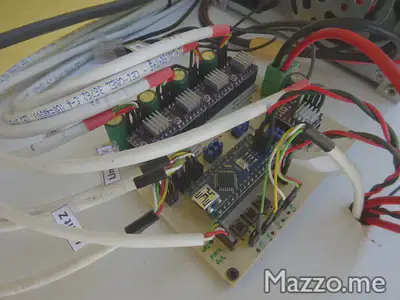
The electronics of the brushless spindle motor was purchased together with the spindle motor itself:
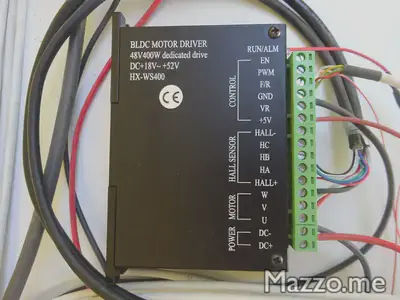
As well as the 48 V power supply:
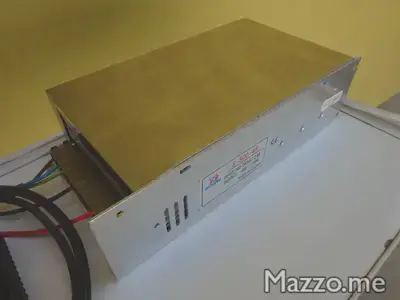
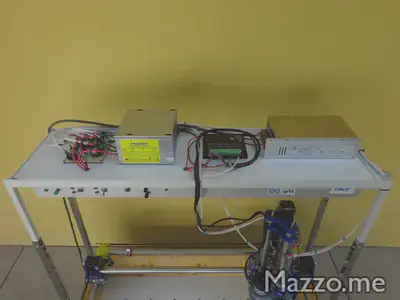
In the work plan I have placed threaded inserts:
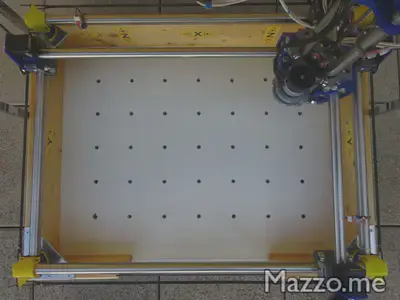
Some of the work I made with my MPCNC: